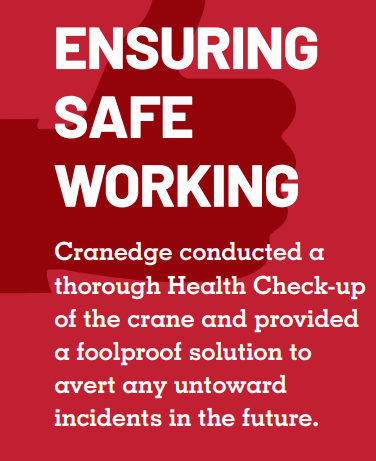
About the project challenges
In spite of good maintenance, certain equipment of old generation technology always poses safety challenges due to inadequate inbuilt protections and safety features.
The Pune Plant of the automotive company encountered a similar challenge with its 25t DG EOT crane. On a usual day, during routine operations, a heavy load was being handled using this crane and suddenly, the load slipped off and fell from a height of 8 metres
Fortunately, there were no casualties, but serious damage was caused to the machinery which resulted in financial losses. The incident created immediate ripples within the company and shook many as the crane posed a real threat to the employees’ safety. Of course, a company, which is known for the care it takes of its employees and its adherence to the highest level of safety standards, took the incident very seriously. A thorough probe was initiated to find the causes of this mishap and it was decided to consult industry experts. When they came across our name, we were called to investigate the reasons behind the accident and suggest as well as implement a foolproof solution which would avoid any such accidents in the future.
Solution from Cranedge
In such incidents, the first task undertaken by the Cranedge team is to investigate the causes. Our preliminary investigation revealed that the failure of the brake of the hoisting motor was the major reason of the accident. Subsequently, our team conducted a thorough Health Check-up of the entire crane including structural analysis (FEA) of the main girder.
A complete report on the present condition of every major component of the crane was submitted to the customer. Also, our recommendations for additional features to ensure higher levels of safety were accepted by them.
We have incorporated various solutions for enhanced safety which include:
- Anti-fall System: This consists of a dual braking system. In case the main brake fails, the standby brake immediately becomes active and can hold the load for about ten minutes. This critical time interval allows the operator to safely lower and park the load at a safe location. Also, in case the main brake fails, the system automatically triggers an alarm/siren warning the operator and the people in the vicinity about the emergency and the possible danger.
- VFD – Variable Frequency Drive: Being an old generation technology crane, it was fitted with a slipring motor and speed controller. The slipring motor has its own limitations and drawbacks as against the squirrel cage motor plus VFD that offers better control, VFD being more energy efficient, also helps in reducing energy consumption. Considering these aspects, we replaced the slipring motor with a squirrel cage motor and VFD.
- Control Panel: The crane is now fitted with a completely new electrical panel housing VFD and other controls.
- Drag Chain: Earlier, the crane was fitted with cable trailing systems that were clumsy and prone to breaking. This is now replaced with more robust drag chain systems.
Benefits to the automotive company
- The objective of this project was to ensure a high level of safety and avert any accident in the future due to malfunctioning. This objective is being clearly addressed through retrofitting a few critical components and incorporating advanced safety features.
- Enhanced crane performance due to addition of a few features such as VFD.
- Enhanced crane life at a marginal cost as compared to investing in a new crane.
Crane and its components after overhauling and repair
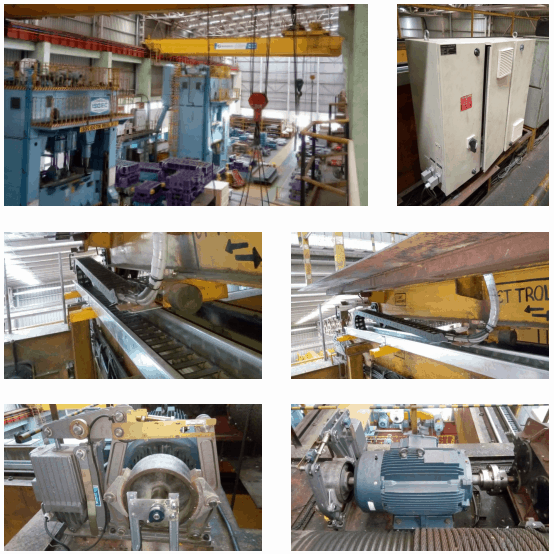
Expert aftersales support for
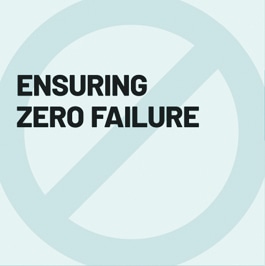
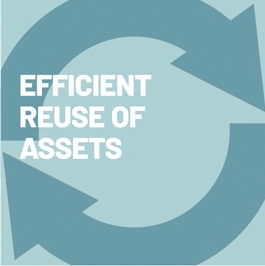
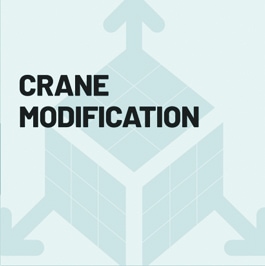

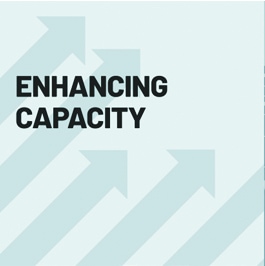

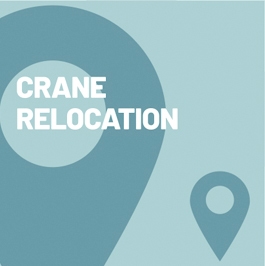
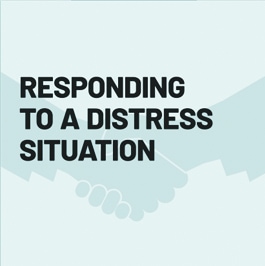
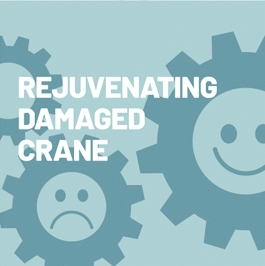

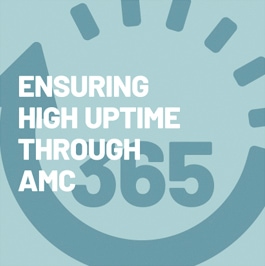
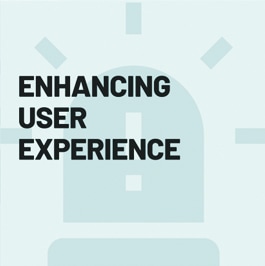
Disclaimer
© Copyright 2020 | All the names and logos used here are the registered trademarks of respective companies. For private circulation only. Certain data mentioned here is based on assumptions and theoretical calculations, hence may not be accurate in practice and can’t be considered as a claim by the company.