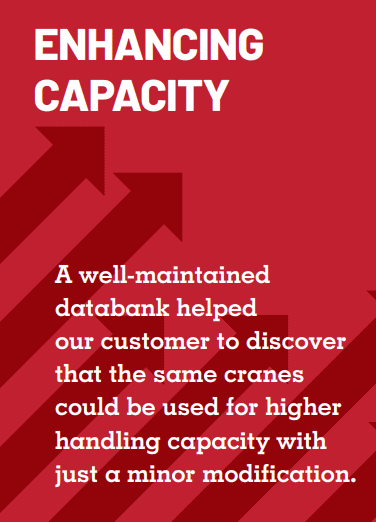
About the project challenges
In the Bengaluru factory, several ElectroMech cranes are being used for a variety of applications ranging from the handling moulds of windmill blades to assemblies of wind turbines and further loading them onto trailers. In its windmill blades manufacturing facility, four ElectroMech cranes are deployed in two bays for handling long moulds. Each of these single girder cranes is of 8t capacity, 20.5m span and 8.5m height of lift. Two cranes work in tandem to lift one long mould.
When the company introduced blades of a new design, the handling requirement changed. The new blades were longer, resulting in the weight of the mould increasing from 16t to nearly 20t. The company’s team thought that they could use the same cranes for the changed requirement by changing the hoisting mechanism and enhancing the capacity of the cranes and hence approached Cranedge.
Solution from Cranedge
Even the smallest of components used during the manufacturing of ElectroMech cranes is traceable. Such data is stored on a Data Management Server throughout the lifecycle of the crane and can be quickly accessed by the ElectroMech and Cranedge teams whenever required.
After knowing the requirement, our experts visited the site to study the new requirement and the details of the existing cranes. Further data mining revealed that being ElectroMech hoists, the 8t hoists used on these cranes are inherently designed for 10t capacity. Then, it was only the structural elements like girders and end carriages that needed to be checked for suitability of load. Reverse engineering of the crane girders confirmed that they too were suitable for 10t loads. However, the end carriages required strengthening as they were designed only for 8t capacity.
Once sure about the solution, our team recommended strengthening of the end carriages and reassessing the entire system for the suitability of 20t load carrying capacity while using 2 cranes in tandem.
This was a much more economical proposition as compared to upgrading the hoisting mechanism and hence delighted the customer. The entire work was carried out during the plant shutdown period and completed in just one week at the site.
A customer is a multifaceted group that is into energy, transport, water and construction related activities. One of its group companies is into the wind energy sector and offers sustainable solutions and energy products in all activities across the energy value chain, which makes it a one-of-a-kind company in the market. The company has a well-equipped factory that manufactures windmill blades and wind turbines near Bengaluru, India.
The group is a long-time customer of ElectroMech and uses several of ElectroMech cranes in their factories and on project sites across India and in the Middle East.
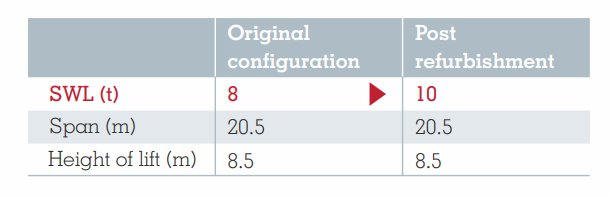
Benefits to the customer
The customer is extremely happy with the solution from Cranedge and benefitted in the following ways:
- Capacity enhancement in a minimal budget due to the rugged construction of ElectroMech hoists and cranes, and the expertise of the Cranedge team in evaluating the requirements correctly.
- The work was completed on-site and swiftly without affecting regular production or without the downtime of cranes during routine operations.
- Assurance of safety through proper assessment and thorough trials after completion of the work.
- Assurance of prompt after-sales service through the team of Cranedge experts.
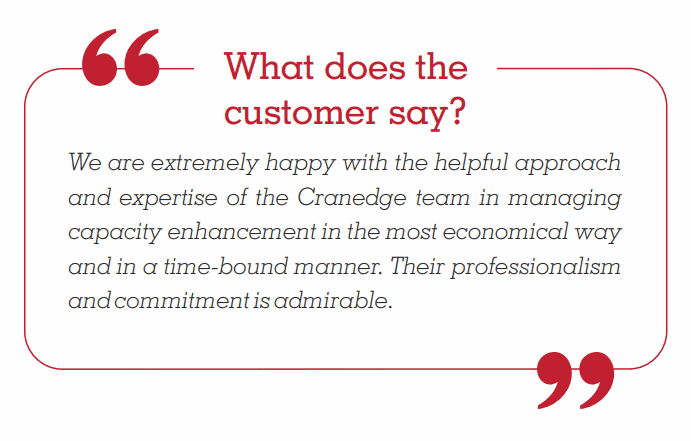
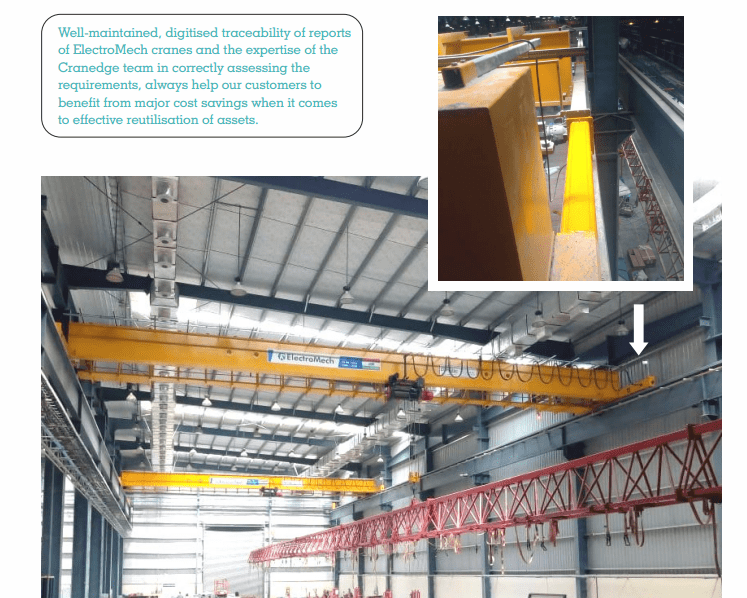
Expert aftersales support for
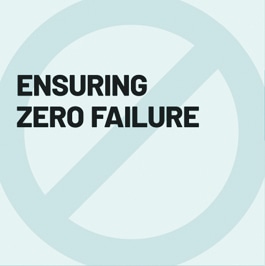
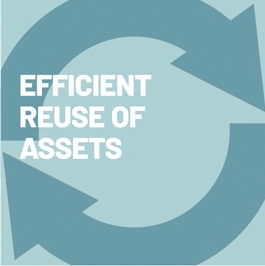
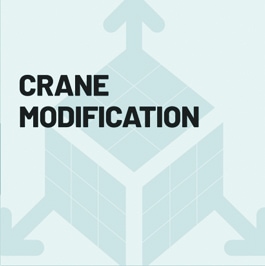

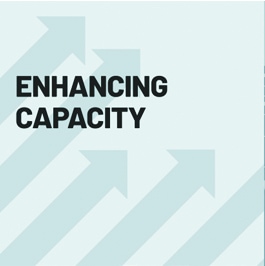

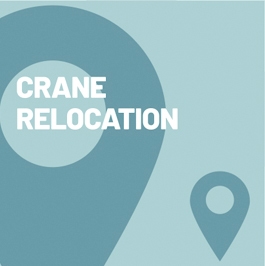
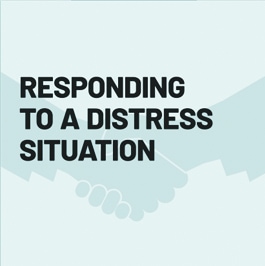
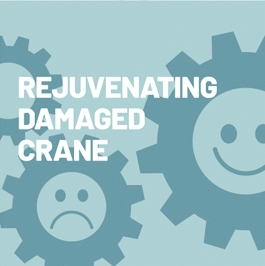

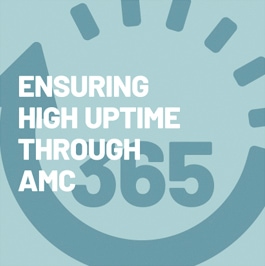
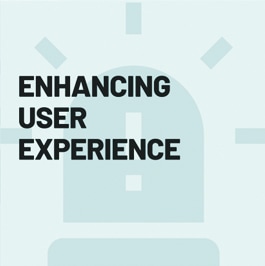
Disclaimer
© Copyright 2021 | All the names and logos used here are the registered trademarks of respective companies. For private circulation only. Certain data mentioned here is based on assumptions and theoretical calculations, hence may not be accurate in practice and can’t be considered as a claim by the company.