Pairing an underutilised crane with the existing one to double the lifting capacity in a gearbox manufacturing plant where it was needed the most
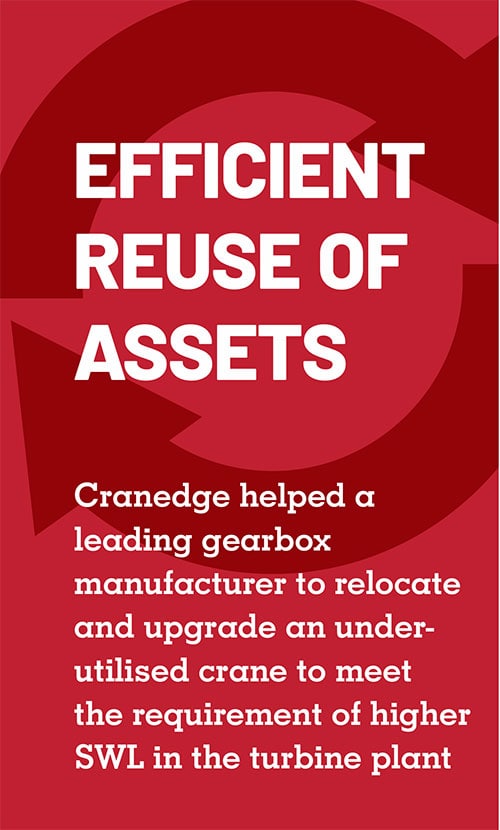
About the project challenges
Earlier, the customer was manufacturing gearboxes for smaller nacelles of windmills. The weight of such gearboxes did not exceed 40t and hence a 45t Abus crane supplied by ElectroMech in 2008 was perfect for the job. Since the market for large-sized windmills is growing, the larger gearboxes are in demand, which are comparatively huge and heavy, weighing around 70t. To handle large, heavy components and gearboxes of larger sizes, it was essential to have a crane with minimum 70t lifting capacity (SWL).
To meet the challenge, the customer thought of the following options:
- To shift the large gearbox manufacturing to a new bay/shed and install a new crane of sufficient capacity
- Procure a completely new crane of more than 70t SWL for the existing bay
In this particular plant, the customer is using more than 170 different types of ElectroMech cranes. All of these cranes are under AMC with Cranedge and we have a permanently stationed team of crane maintenance experts to ensure seamless service support. During the routine review meeting with the Cranedge team, the customer voiced the changed requirement, the challenges posed and asked our team for advice.
Solution from Cranedge
The customer was looking for a cost-effective solution that would be quick to implement. While resonating with this approach, the first and foremost thought of our team was to make use of an underutilised crane from the fleet of the existing 170 cranes – a solution that would be economical, simple and could be implemented immediately. Our team quickly assessed the new requirement and began evaluating whether there were any underutilised cranes that could be relocated.
Being conversant with the locations and usage patterns of all the cranes in the plant, the job was easy. Additionally, our proprietary software tool, Computerised Maintenance Management System (CMMS), came in handy to help us narrow down the search. CMMS maintains all the data related to each crane, including its usage pattern over the years. Using CMMS, the team soon identified that there was a 45t crane in one bay, which was underutilised and had identical specifications as that of the crane in the gearbox assembly bay. The idea was to relocate this underutilised 45t crane and pair it with the existing 45t crane. This would enhance the lifting capacity to 90t.
Though the solution sounded simple, its implementation was challenging for two reasons –
- The load-bearing structure of the existing bay was designed for a 45t capacity crane
- To lift the load of 70t using two cranes, it was essential that they must be synchronised for tandem operation
We could overcome these challenges by spacing the two cranes appropriately. This ensures that the wheel load of both the cranes is distributed over the gantry and column structure and does not exceed the limit at any given time. To ensure proper distance between the two cranes, they are provided with sensors and an anti-collision device.
The hooks of both the cranes are connected using a lifting beam resulting in an effective SWL of 90t. The gearbox assembly is suspended to the beam while handling. The cranes fitted with new electricals and control panel. Both the cranes are electronically coupled to form a pair, thus ensuring synchronous movement.
Additional features, such as VFD controllers, load limiter devices and load summation devices are added to further enhance safety.
Benefits to the customer
- Saved major cost which would otherwise be required for
- procuring a new crane
- enhancing the structural strength of the existing shed or constructing a new shed
- Efficient reuse of existing underutilised assets
- Procurement process, purchasing and actual delivery of a new crane would mean a loss of four months, whereas the relocation and refurbishment work was completed in just two months
- Higher level of safety through refurbishment of both the cranes and addition of safety features/devices
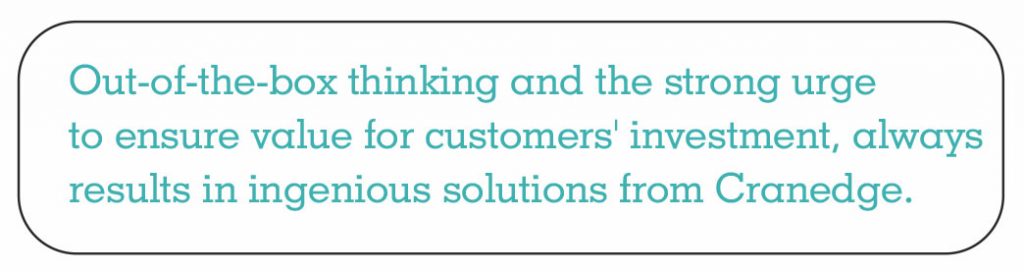
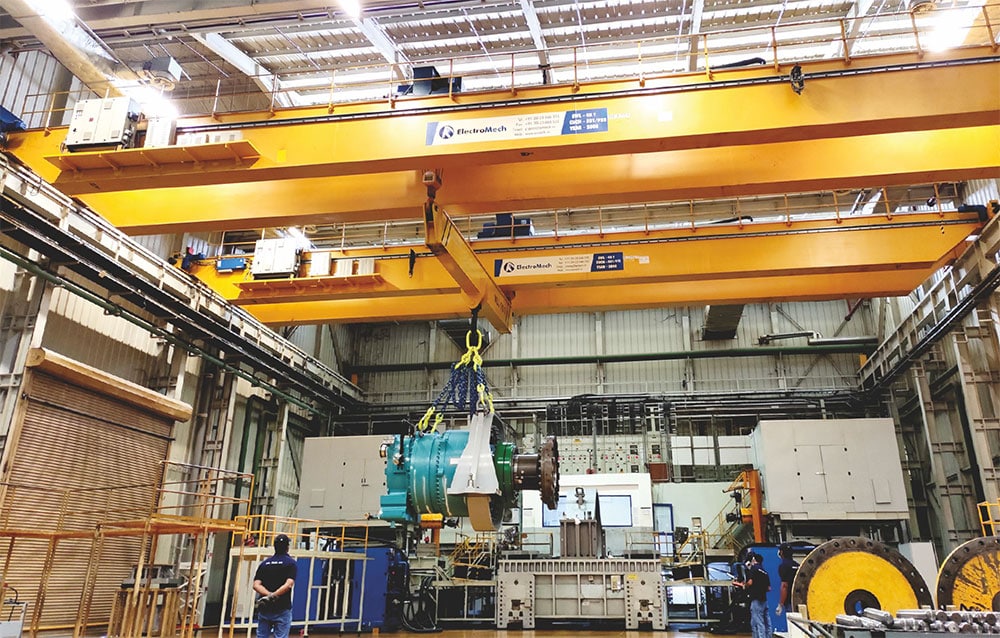
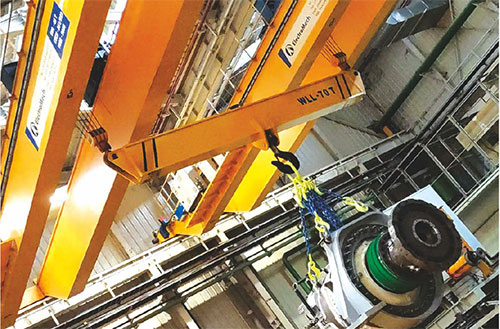
Disclaimer
© Copyright 2020 | All the names and logos used here are the registered trademarks of respective companies. For private circulation only. Certain data mentioned here is based on assumptions and theoretical calculations, hence may not be accurate in practice and can’t be considered as a claim by the company.